首钢建设智慧工厂的探索与实践
专题协办:达涅利冶金设备(中国)有限公司
针对智能化发展与钢铁产品质量、工艺控制、设备管理等业务不同程度脱离的共性问题,首钢以制造、管控和研发效率提升为目标,以数据协同和多目标决策为手段,以业务流程优化和应用落地为导向,在轧制工序优先探索建设智慧工厂,全面推进效益、效率及客户服务能力的提升。在京唐热轧,以CPS智能运管平台为核心,着力于质量、工艺与设备的监控、诊断、分析、溯源、优化等的全生命周期智能化建设;在首钢股份冷轧,进行面向供应链和工厂制造的横向、纵向集成建设。智慧工厂的示范试点建设为首钢逐步推进制造与管理的创新变革积累经验,更为全面建立“操作自动化、管控集成化、设备智能化、物流信息化、生产柔性化、工厂数字化、决策智能化”的智能制造新格局打下基础。
1前言
首钢集团作为中国钢铁工业最具竞争力的企业之一,较早实现了全流程工序的自动控制,建立了从基础自动化层到经营管理层的信息管理系统,具有钢铁行业领先的自动化与信息化水平。同时,首钢集团在自动化、信息化和两化融合过程中,对工业互联网、云计算、大数据等信息技术持续跟踪和实践运用,具备开展智能制造创新的技术基础。
钢铁行业具备生产流程长、生产工艺复杂、供应链冗长等特征,面临设备维护低效化、生产过程黑箱化、下游需求碎片化、环保压力加剧化等痛点,正以工艺优化为切入点,加速向设备运维智能化、生产工艺透明化、供应链协同全局化、环保管理清洁化等数字化、智能化方向转型。根据国家智能制造试点工作和专项工作要求,结合自身智能制造工作规划,首钢集团提出“绿色制造、智能制造、精品制造、精益制造、精准服务”的总体工作思路,将智能制造确定为重要发展方向之一。以智慧工厂建设为重要主线,通过物联网、云计算、大数据、人工智能等新技术与工艺和管理深度融合,在重点工序进行探索实践,打造出具备“状态感知、实时分析、自主决策、精准执行、绿色安全”特点的工业智能化系统,达到生产的最优化、流程的最简化和效率的最大化。
2京唐热轧智慧工厂探索与实践
如何实现质量更优、成本更低、效率更高和服务能力更强,是钢铁智能制造转型发展的核心任务。热轧作为钢铁流程中自动化程度最高、控制变量最多、功能最复杂的环节,在大数据和互联网平台等技术的快速推进中,无疑是智能制造“示范先行”的热点工序。但无论是首钢还是其他钢铁企业,在轧制智能化的推进过程中都遇到了“数据协同”与产品质量、工艺控制及设备管理等业务不同程度脱离的共性问题,主要体现在:1)大量基础数据难以回流到底层控制形成闭环,难以与工艺深度协同;2)制造单元的主要过程数据还未实现采集、归档并开发,难以支撑建立生产智能化和协同决策的“云-边-端”体系架构;3)底层控制依然存在大量人工操作、系统黑箱及状态感知瓶颈等问题,
依托于现场实际痛点,立足工艺精细化控制和设备潜能挖掘,自主研发了CPS质量与设备大数据管控平台。通过搭建涵盖过程质量控制、设备运行状态和生产制造状态等基础数据的边缘侧数据平台,以板形、温度、宽度等为窗口,打通了面向生产稳定性、质量一致性和综合协调优化的多目标智能决策和协同控制壁垒,为提升整体制造效率和质量效益,并形成标准化、模块化、可移植的数字化工厂构架做好技术支撑;并基于边缘侧数据开发了不同业务需求的功能模块,内容涉及生产计划跟踪、轧制过程监控、设备信息管理、设备状态监控、工艺功能管理、生产综合报表、质量溯源分析、过程质量诊断、大数据驾驶舱、VR虚拟仿真、移动端APP等相关业务。
CPS平台目前实现了整体架构搭建和设备信息管理功能模块的上线部署,及时反映设备体系状态,实现设备资产价值最大化和生产计划的正常执行;实现了工艺功能管理的测试发布,对功能精度、过钢通道、刚度、工艺水喷嘴以及技术操作事故等综合性管理,提供有效的决策支持;实现了质量大数据、轧制状态报警以及精轧机设备诊断驾驶舱的初步开发;实现了质量溯源分析、过程质量诊断、生产综合日报以及移动端APP相关功能开发测试。后续将持续推进热轧工序点自动化数字化的“填平补齐”,做到可控、可自主优化升级,为单工序及上层多目标协同优化做好支撑;利用大数据平台进行单工序质量缺陷诊断、多工序耦合质量评价等系统开发,建成一系列面向质量稳定性和高精度提升的优化集群工具和一键式解决方案,支撑各业务需求的落地实施;完善生产综合月报,实现囊括生产管理、质量管理、设备管理、成本管理、指标管理以及安全管理等的查询统计和报表生成。同时,将在VR虚拟仿真以及过程诊断优化集群等领域助推京唐智慧热轧全景生态,实现支持移动端APP的质量实时跟踪、设备状态监控、保养维护、故障诊断的全生命周期管理,不同岗位根据权限分配分级推送业务内容,推动京唐热轧全生命周期数字化“智慧工厂”建设。
如图1所示,随着CPS质量设备智能管控平台的搭建,从梳理现场各项业务需求,到完成业务框架搭建,直至目前系统上线内测。生产、工艺、物流、服务等各项业务驱动并不关心系统架构和底层平台形态,应用层设计和“数据应用”的赋能过程才是整个智能制造的关键。通过对设备的技术状态全生命周期管理,及时反映设备体系状态,实现了设备资产价值最大化和生产计划的正常执行;通过个性化的生产综合日、月报一键分析模块,实现了囊括生产管理、质量管理、设备管理、成本管理、指标管理以及安全管理等的查询统计和报表生成。在平台建立之前,统计一页综合日报需要一名技术人员花费数小时才能汇总出来,有时还会因过程偏差带来数据可靠性问题,平台建立之后任何授权用户可以在秒级内精确生成综合日报;通过工艺功能管理,实现对功能精度、过钢通道、刚度、工艺水喷嘴以及技术操作事故等的综合性管理,提供有效的决策支持;通过质量溯源分析和过程质量诊断,形成一系列面向质量稳定性和高精度提升的优化集群工具和一键式解决方案,进而实现工序间或工序内部窗口如板形、温度、宽度等的智能决策和协同控制。不仅能够大幅降低人力对数据统计及分析的消耗,而且可对生产中棘手的、事后分析才发现的质量问题进行及时诊断和预警,并提供相应的优化策略建议,更加精准地实现质量问题的控制与处理。这项工作需要开发者具有深厚的工艺模型功底和积累,对产线棘手的、难点的问题进行精准判断与溯源,也正是CPS质量管控分支的核心意义所在。通过客户端、手机app、小程序等不同应用形式的技术开发,实现不同岗位的权限分配和内容分级推送,探索首钢热轧全生命周期数字化“智慧工厂”建设路径。
图1 “智慧工厂”多目标分层建设路径
流程型工厂数字化和智能制造技术还在百花齐放的探索发展之中,在关注顶层设计的同时,更要注重考察各项实践的实际效果。后续将持续推进热轧工序点自动化数字化的“填平补齐”,做到过程可控、可自主优化升级,为单工序及上层多目标协同优化做好支撑;利用大数据平台进行单工序质量缺陷诊断、多工序耦合质量评价等系统开发,建成集群式应用组件,支撑各业务需求的落地实施。同时,将在VR虚拟仿真以及过程诊断优化集群等领域助推京唐智慧热轧全景生态,实现支持移动端APP的设备状态监控、保养维护、故障诊断的全生命周期管理,持续推进京唐数字化钢厂建设。
CPS不是单纯的信息化系统开发,应用层设计和大数据的赋能过程才是整个平台落地的关键,真正能够研发出落地有效的智能管控技术,需要培养出具备丰富的业务知识和信息化、智能化技术融合的优秀队伍。CPS质量与设备大数据管控平台,有利于技术落地与应用发展,是对流程型工厂数字化和智能制造技术的一次有益的探索。不断的平台技术完善和应用拓展必将导致企业重构升级现行的运行模式,从效率、效能和质量上为企业带来颠覆性的影响。
3首钢股份冷轧智慧工厂探索与实践
结合硅钢冷轧生产特点,深度分析首钢在智能制造和智能管理方面的差距,查找工厂智能管理的瓶颈和痛点。遵循整体性、先进性、开放性、经济性和规范性等原则定位工厂顶层设计。科学定向,对涉及硅钢冷轧生产的全流程、全业务进行梳理,确定优化和创新整改方向。以大数据、物联网和智能化技术管理手段为向导,坚持绿色制造的理念,以决策科学化、服务增值化、研发数字化、生产柔性化、质量精准化、操作无人化为目标,通过智能化建设和智能管理水平提升,实现技术突破、业务变革,管理创新,并实现经济指标实质性的提升。
在智能决策层,通过融合国内大数据建设技术方案和实践案例,建设大数据机房,满足系统开发硬件基础。实施对全工艺流程和生产过程的基础数据采集和数据治理。构建生产经营KPI体系,结合冶金行业通用指标及硅钢冷轧生产特有指标,构建包含制造、技术、质量、营销、设备、安环共六大类、十个管理方向、103个管理指标的生产经营KPI体系,在管理驾驶舱系统直观展现生产过程中,各机组的产量、生产库库存、制造成本、设备运行状态监控等几方面,实现考核指标模型化。为公司高层管理人员直观、高效地监控硅钢冷轧的生产运营状况,实现合理管控与风险控制提供支撑。
在产销研智能协同方面,结合硅钢冷轧客户EVI技术,将产品研发与客户需求紧密结合,借助于大数据和知识库等手段,搭建硅钢冷轧产品研发平台,实现产品研发数字化,实现产品研发设计流程的再造。通过基于产品EVI及知识库建立产品智能设计知识库,并在此基础之上构建基于DFSS的产品智能研发体系,实现产品研发显性知识与隐性知识的集中管理、产品设计要素的可视化分析、缩短研发周期、精确识别客户需求并引领市场需求的新产品智能设计,如图2所示。搭建硅钢协同制造管理系统以硅钢冷轧产品运营协同为核心,支撑硅钢冷轧产销衔接、订单管理、质量设计、计划排程的业务协同,实现营销管理、生产管理、技术质量管理等管理部分职责协同。通过采用构造启发式方法,针对不同计划特点,分别搭建k-means聚类方法、离散差分进化算法、差分进化算法等模型,支持系统实现自动计划排程,减少计划人员日常工作,提高效率。从客户需求出发,引入精益供应链管理和最新客户体验理念,站在客户视角驱动流程优化,建立数学模型,构建B2B的一贯制精准服务平台。面向客户提供产品销售全流程自助服务,提升客户体验;面向销售提供市场资源预报分析及销售策略制定,提升企业营销能力;面向客户服务提供售前产品推荐、售中订单跟踪、售后质量异议、物流等数据推送,提升客户服务水平。
图2 营销服务实施思路
在全生命周期产品质量管控方面,完善各工序质量信息,增大质量信息颗粒度,对多工序关联数据进行整合,做好质量管理数据基础;依托硅钢冷轧产品的性能预测模型建立工艺控制标记体系,优化排程,缩小成品质量波动区间,实现生产过程的动态质量设计、精细化质量控制,满足用户的个性化需求;针对硅钢冷轧产品从客户需求、产品开发、制造、物流、客户使用、废料回收进行质量跟踪、监控,实现产品全部生命历程的质量管理。实现产品质量全程可控,对于异常状态可以进行实时监控与调整,达到品质最优化,降低废品率及改判率。在线质量判定实现自动检测判定,缺陷判定时间和质量判定时间成倍缩短,判定准确度大幅提升;运用智能工厂大数据分析技术,将产品全流程各生产工序的尺寸、性能、表面类综合判定结果进行准确定位到最终精整分切工序的带钢全长,同时结合客户的订单要求,指导岗位自动执行智能分切,改变传统通过人工分析给出分切结果的方式,实现对成品卷精准分切。质量工程师借助数字化、模块化的管理工具,按照质量改进支撑、质量过程强化控制、质量设计补充的管控流程推动实现全生命周期产品质量管控。
目前首钢股份公司已建立针对30多个硅钢冷轧品种划分的300多条原料标记、800多套设定工艺,并形成2万多套制造标准,有利支撑硅钢冷轧产品的动态质量设计。在线自动质量判定系统缺陷判定时间缩短为原来的六分之一,质量判定时间缩短到1分钟以内,判定准确度提升到95%。特别是缺陷智能分切技术领先于国内对标厂家。截至目前硅钢冷轧产品综合智能分切比例达96%以上。随着质量智能管控能力的的提升,首钢硅钢冷轧产品尺寸精度,铁损、磁性能等关键指标均达国际先进水平,得到客户一致认可。同时协议带出品率持续降低,产品盈利能力显著增强,产品竞争力大幅提升。
在装备智能化方面(见图3),结合硅钢冷轧制造过程工艺流程及产品特点,应用新技术和新理念,实施物流仓储智能化升级,生产运行的智能视频监控改造,研发了智能化硅钢冷轧原料物流转运管控系统。该系统综合利用现代信息技术、智能感知等多项新技术,实现物流车辆进出库自动导引及管控、钢卷ID在线自动识别检验等自动化操作,规范原料物流转运业务流程,降低了原料库管理岗位的劳动强度,打通了酸轧原料转运到上料整个流程的信息流,形成酸轧原料转运至上线信息的一体化、智能化操作。硅钢冷轧样板自动取样、制样及磁性能自动检测系统利用机器人装备实现取样过程样本的“自动输送、自动分拣码垛、激光二维码标识”、自动插片磁性能监测,样板收集等无人化操作。真正实现了从毛坯样板分拣加工和磁性能检测的全过程自动化。结合硅钢冷轧制造工艺在不同工序段的特点,研发了拆捆带机器人、机器人自动储运套筒系统、贴标机器人、钢卷内圈固定点焊机器人、取样机器人五种不同类型的工业机器人用于实际生产现场,提高生产作业效率,保证了人员安全,同时为现场生产人员调配和人员管理提供了便利。
图3 轧后库智能仓储(无人天车)
在设备状态智能诊断方面,冷轧智能工厂设备监测与智能诊断系统监测范围覆盖硅钢冷轧生产的200多台关键设备,新增振动、温度等400多个监测点,集成整合已有的液压、电气等各类监测量1200多个。设备管理实现从“人工离线点检”到“远程在线监测”,从“信息孤岛”到“设备状态大数据平台”,从“事后人工分析”到“系统智能诊断”的设备管理变革。
通过以上仓储物流的优化、自动化功能升级、智能视频监控、智能装备及设备状态诊断系统,有效规避操作风险,降低劳动强度。在此基础上实现业务优化、运维的集中。生产操作模式从现场多点位操作分散监控到自动运行集中监控,工作重点从关注操作运行到监控运行专注工艺质量管控。实现了生产管理质的变革,实现了人员和操作的集中,并进一步整合业务,提升管理效率。真正实现了减员增效。
4总结
首钢集团在钢铁板块的智能化创新和实践,通过工业互联网、工业机器视觉、工业机器人、5G通信技术、云计算、数字仿真模型及工业大数据挖掘等智能制造技术的应用,达到安全、环保、生产、质量、设备、成本、能源、物流、管理效率集中协同高效,以产品作业效率、质量、成本为主线,正在构建出实时互联、柔性制造、高效协同、价值共享的钢铁智慧制造服务体系。在提升企业综合竞争力的同时,为实现国家制造强国的目标贡献力量。到2025年,首钢集团智能制造发展将重点落地,制造体系更加完备,供应链协同更加高效,工艺智能控制更加先进,大数据价值发挥显著提升,关键新型信息基础设施应用更加广泛。依托集团管控、产销一体化、智能管控等信息平台,通过各项共性支撑新技术的应用,挖掘物料、装备、人员、环境、产品、服务渗透协同的数据价值,在促进研发创新、提高产品质量、降低运营成本、提高作业效率、提升服务能力、坚持绿色发展、实现本质安全方面起到关键支撑和引领作用,全面建立“操作自动化、管控集成化、设备智能化、物流信息化、生产柔性化、工厂数字化、决策智能化”的智能制造新格局。
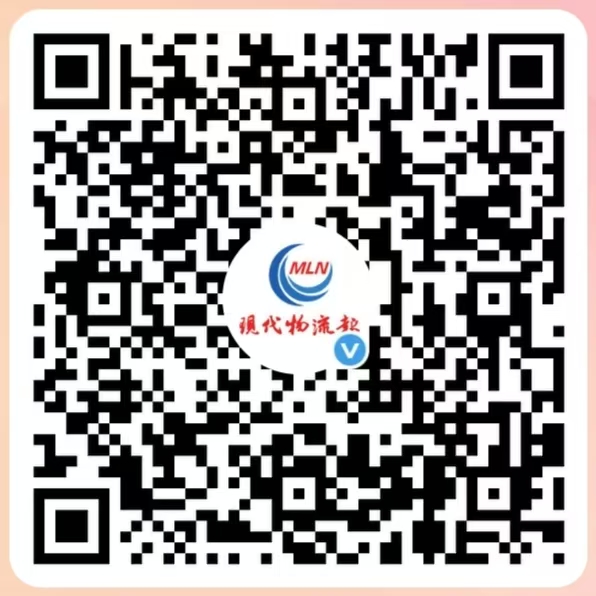
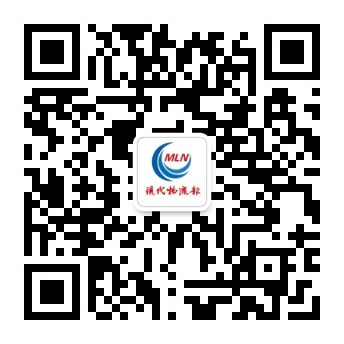
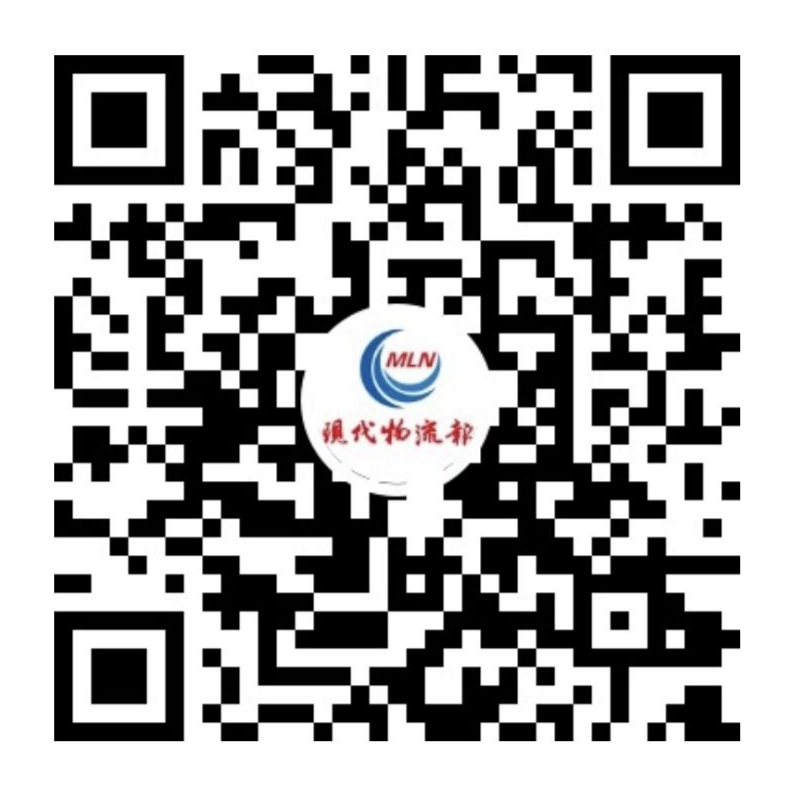
相关文章: