《记者走一线——数字化转型典型案例企业巡礼》
鞍钢关宝山矿业:黑灯工厂建设让选矿作业实现革命性改变
选矿是钢铁工业中一道重要工序,铁矿石经过球磨成粉状,再经浮选、磁选等选矿工序将铁元素富集,得到铁精粉,再由造块工序(烧结或球团)生产为块矿,才能作为高炉炼铁的原料。众所周知,我国铁矿石资源丰富,但是富矿少、贫矿多,所以选矿工序就显得尤为重要,如何提高选矿工序的效率,如何从有限的原矿中筛选出更多的精矿,对于我国钢铁工业有着特殊的意义。
是否能将数字科技应用于选矿流程,实现选矿过程的智能化、机器人化,进而改善我国资源状况,并实现钢铁工业降本增效?对于这个问题,鞍钢集团关宝山矿业有限公司(以下简称“关宝山矿业”)近年来勇于尝试,对智能选矿进行了大量积极的探索,并取得了丰硕的成果和宝贵经验。
近日,中国金属材料流通协会联合《现代物流报》共同采访了关宝山矿业副总经理刘春辉,了解了数字科技给选矿生产带来的巨大改变。
在选矿作业中
实现“黑灯工厂”
关宝山矿业有限公司位于辽宁省鞍山市,隶属于鞍钢矿业,是集采矿、选矿为一体的现代化采选联合企业,是鞍钢集团重要的铁精矿生产原料基地之一,拥有两座铁矿山和一座选矿厂,原矿处理能力为每年600万吨,每年可生产铁精矿175万吨。
关宝山矿业建于2012年,公司起点较高,成立之初就配备了国内最先进的选矿产线设备。但是鞍钢矿业对于关宝山矿业的期望较高,并不满足于传统的自动化生产。在传统生产模式下,生产设备的启停、生产质量的控制,仍然需要大量工人在生产现场操作。工人需要在嘈杂的厂房内,在巨大的设备间爬上爬下。这样的生产不但工人劳动强度依然很大,而且效率、产品稳定性较低,间接损失较高。
从2019年开始,关宝山矿业启动了基于数字科技的选矿智能化建设,并在2022年实现了“黑灯工厂”的建设目标,让生产过程发生了革命性的改变。这种改变主要体现在五方面:
第一,实现生产的远程操作。
公司建立了生产集中管理中心,让原有生产工序中需要现场操作的工作全部实现了远程电脑一键操作,从而基本实现了操作现场的无人化。
第二,实现生产管控智慧化。
公司不仅实现了生产的远程操作,在很多环节还实现了智能化无人操作。借助大数据、边缘计算等技术,公司实现了生产管控的智能化,在磨矿、浮选等关键工序,都实现了智能优化控制,实现了集团“精细管理,颗粒归仓”的要求。
比如在铁矿石选矿过程中对矿浆浓度和品位的检测,以前人工检测化验容易产生误差,对操作员的经验技能要求较高,且检测周期较长。如今智能检测系统可自动对矿浆进行24小时测量,误差率仅为1%,而且检测化验的时间缩短为以前的1/60。
此外对浮选工序进行智能化改造后,选矿厂还实现了对原矿的更高效利用。在改造后的产线上,经选矿后的精矿品位合格率提高了10%以上,尾矿品位则从21下降到了19.5以下,更多宝贵的铁元素进入到了下游冶炼环节。
第三,实现设备运维智能化、远程化。
要实现生产现场无人化,除了设备操作,还需要在设备维护上实现智能化。关宝山矿业在所有生产设备上都安装了传感器,通过对设备电流、电压、温度等指标的24小时监测,并基于大数据模型,可对生产设备进行远程的智能隐患排查、智能故障分析。同时结合巡检机器人的24小时巡查,使以往工人现场检查设备的工作大大减少,巡检效率提升了80%以上。
第四,以综合感知为保障,实现生产安全本质化。
公司还利用视频传感器和基于AI视频的分析技术,建立起了“电子围栏”,对矿山、厂房内的危险违章行为实现智能监管。该技术的应用让以往现场人员的不安全行为无法被及时发现、及时提醒和快速处置的难题得到了彻底解决。如工人不戴安全帽等危险行为,如今在巡检机器人的监测下,基本杜绝。
第五,实现能源消耗的智慧管控。
以前选矿厂运行过程中消耗的水、电、煤、蒸汽等能源、资源,全靠人工抄表进行统计,关宝山矿业在进行数字化转型后,建立了能源管理系统(EMS),运用物联网、大数据分析技术,实现了选矿生产全流程、全要素能耗数据的采集、计量和可视化检测。同时能源管理系统可以结合当地电能的峰平谷时间段、费用,能耗工序,环境温度等因素进行智能分析,为生产提供用能指导,实现高效用能,降低用能成本。
第六,通过跨业务、跨岗位融合,实现业务流程一体化。
公司以RC管控中心为中枢,把生产全过程中的计划、质量、设备安全等多项业务管控,贯穿于多个业务部门,实现了跨业务,跨岗位的垂直化管控模式。
成为数字化转型标杆
经过选矿智能化建设,关宝山矿业生产服务类岗位的数量减少到了智能化建设前的10%,管理岗位减少到了智能化建设前的47%。
刘春辉介绍,机器人和人工相比,在有些工序上单位小时的工作效率并不一定明显胜出,但是机器人的优势是可以24小时不间断工作,所以总的效率要明显优于人工。现在公司生产过程中的每个细小环节的耗时平均减少了5分钟,所有这些细小环节加起来后,效率就有了明显提升。智能化改造后公司年产量增加达5.8万吨,精矿产量增加1.7万吨,年增收达1000万元以上。
智能化建设通过降本增效和对能源消耗的智慧化管理,让生产过程中的能耗也得到了明显降低,电力单耗降低了2.4%;煤单耗降低了6.4%;综合能耗下降了7.94%。
数字化、智能化给公司带来了明显改变,但关宝山矿业在数字化转型的过程中,也曾面对不小的困难。
第一,职工思想转变难。
近年来,生产的智能化、数字化,对于家电生产企业而言已经是很自然而然的事情了,但是对于像关宝山矿业这样的传统矿山企业来说,依然会有员工不能理解、不愿接受。一些员工觉得搞数字化意义不大,还有些员工担心机器人的应用会影响自己的工作岗位。
针对这些问题,关宝山领导层采取的对策是多带职工去先进的制造业企业参观、学习。要通过参观让大家看到,生产的数字化、智能化所带来的高效率、高效益,看到未来工业发展的趋势。
此外公司也积极做员工的思想引导工作,让大家认识到公司的目标是让机器人和人类各施所长。机器人的作用是让人流向更有价值的岗位,而非失去岗位。
第二,没有经验可以借鉴。
在选矿生产中应用智能化技术,这以前在国内是没有先例的,而国外很多矿山都没有选矿厂,也就更没有成熟经验可借鉴了,所以关宝山矿业所做的事情完全是从0到1的行业探索,需要克服种种预想不到的困难。但也正因如此,其创新价值就更加宝贵。
今年以来,关宝山矿业几乎每个月都要接待三到五家同行企业来参观学习。到访的同行大多感觉很受冲击,他们没有想到矿山企业也可以像家电企业一样,做到如此先进的无人化、智能化。
继续挖掘大数据价值
保持行业技术领先
今年,关宝山矿业公司已经实现“黑灯工厂”的建设目标,但公司数字化的脚步并不会停歇,未来公司计划继续在预制维修体系、数据治理、智慧选矿三个方面进行技术攻关,为中国钢铁工业智能选矿积累更多宝贵经验。
第一,构建全系统的预制维修体系。
关宝山矿业公司认为,从黑灯工厂向智慧工厂跨越,设备的运维管控依然是技术难度较高的事情,特别是在设备维修上,一些工作机器人依然不能完全取代人类。下一步公司将在实现产线的预制维修上进一步加强,要建立从感知、诊断、运维到改善的一体化设备保障新模式。公司将把设备诊断的人工经验和知识转变为大数据模型,让智能系统可以像中医给患者诊断的“望、闻、问、切”一样,实现对设备隐患的更有效的预测和运维。
第二,持续完善数据治理工作。
数据资产是未来选矿工作的根本出发点,也是下一步关宝山矿业的重点工作。在实现数据上云的基础上,未来,公司要从有数据到数据有效地发挥更大价值的方向进一步努力,进一步加强以业务为导向,构建数据模型。实现单点到多点的联动控制和分析。借助大数据模型,实现更低的运营成本和更高的运营效率。
第三,持续打造智慧选矿的技术优势。
未来,关宝山矿业还将立足世界格局和国家战略,继续深耕智能选矿技术的研究,紧密围绕生产的痛点和难点,前瞻性开展不确定性和复杂性的研究,打造智能选矿技术的策源地。
随着国际经济环境趋向复杂,未来我国经济要持续保持高质量发展,要保持供应链的安全、韧性,需要面对的挑战将更加艰巨。越是这个时候,中国企业越需要将数字科技的作用发挥于产业链的更多环节中。在这方面,鞍钢关宝山矿业公司不断探索的精神值得借鉴。
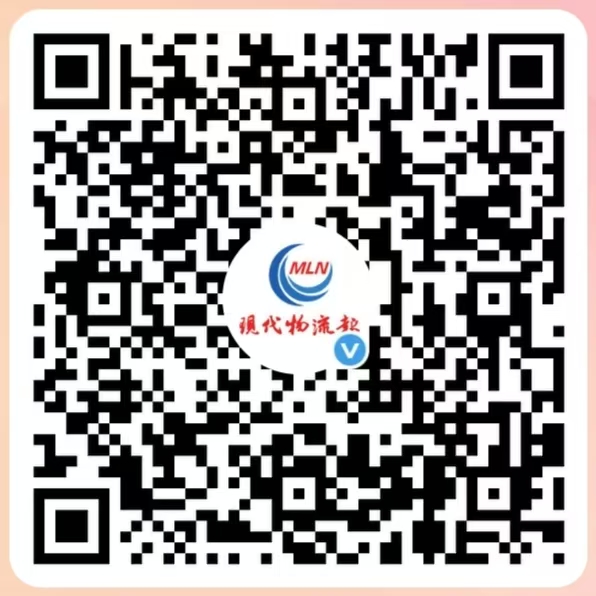
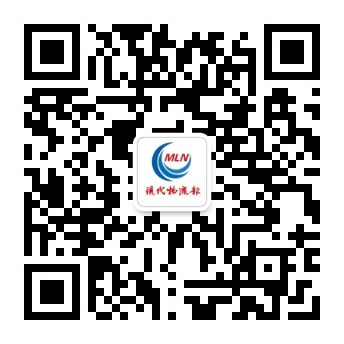
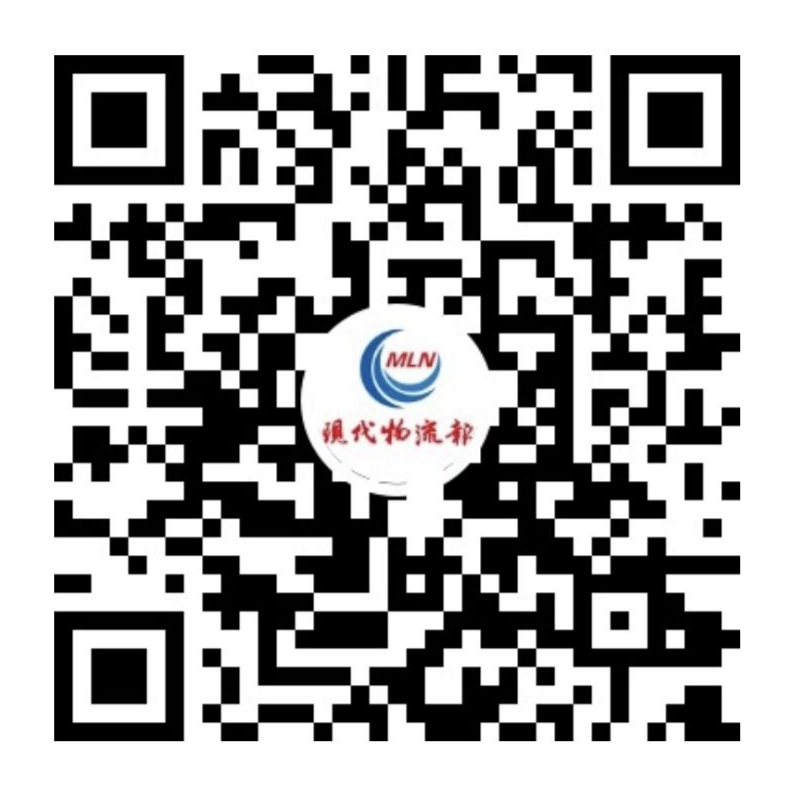
相关文章:
相关推荐: